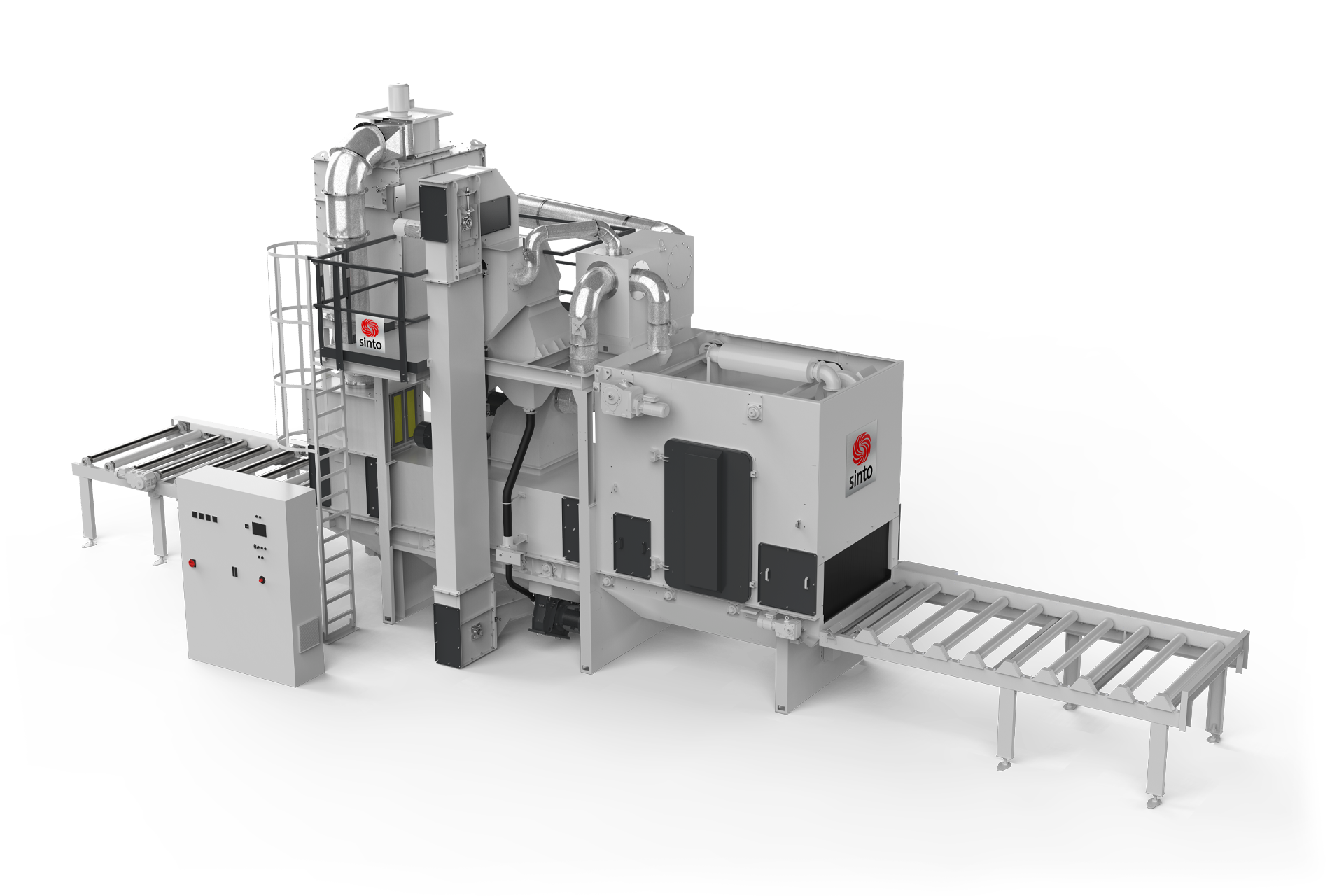
Possible applications of AGTOS roller conveyor blast machines (type RT)
AGTOS roller conveyor blast cleaning systems are ideal for derusting steel beams and descaling profiles and sheet metal. A roller conveyor system, combined with corresponding cross conveyor units, allows individual production stages such as blasting, preservation, sawing and drilling to be interlinked. This ensures a flexible production process and a high material output. Another area of application for the roller conveyor blasting system is the blasting of structures. The turbine arrangement and the throughput openings are precisely matched to geometrically demanding workpieces.
You are currently viewing a placeholder content from YouTube. To access the actual content, click the button below. Please note that doing so will share data with third-party providers.
More InformationRoller conveyor shot blast machines Product programme
Type: | RT 05-10 | RT10-06 | RT15-06 | RT15-10 | RT21-06 | RT26-06 | RT26-10 | RT32-06 | RT32-10 | RT36-06 | RTXX-XX | |
---|---|---|---|---|---|---|---|---|---|---|---|---|
Number of high-performance turbines | pcs. | 4 | 4 | 4 | 4/8 | 4 | 6 | 8 | 6 | 8 | 8 | Nothing suitable? We would be happy to develop a customised solution with you. |
Max. workpiece width | mm | 500 | 1000 | 1500 | 1500 | 2100 | 2600 | 2600 | 3200 | 3200 | 3600 | |
Max. workpiece height | mm | 1000 | 500 | 600 | 1000 | 600 | 600 | 1000 | 600 | 1000 | 600 | |
Throughput speed | m/Min | depending on the blasting task |
Operating sequence for roller conveyor shot blast machines
The diagram on the left shows the path of the workpieces through the AGTOS blasting system. You can count on us to always consider the optimal solution for your workpiece. In doing so, we take into account the factors of time, cost and material. This is how you optimise your production.