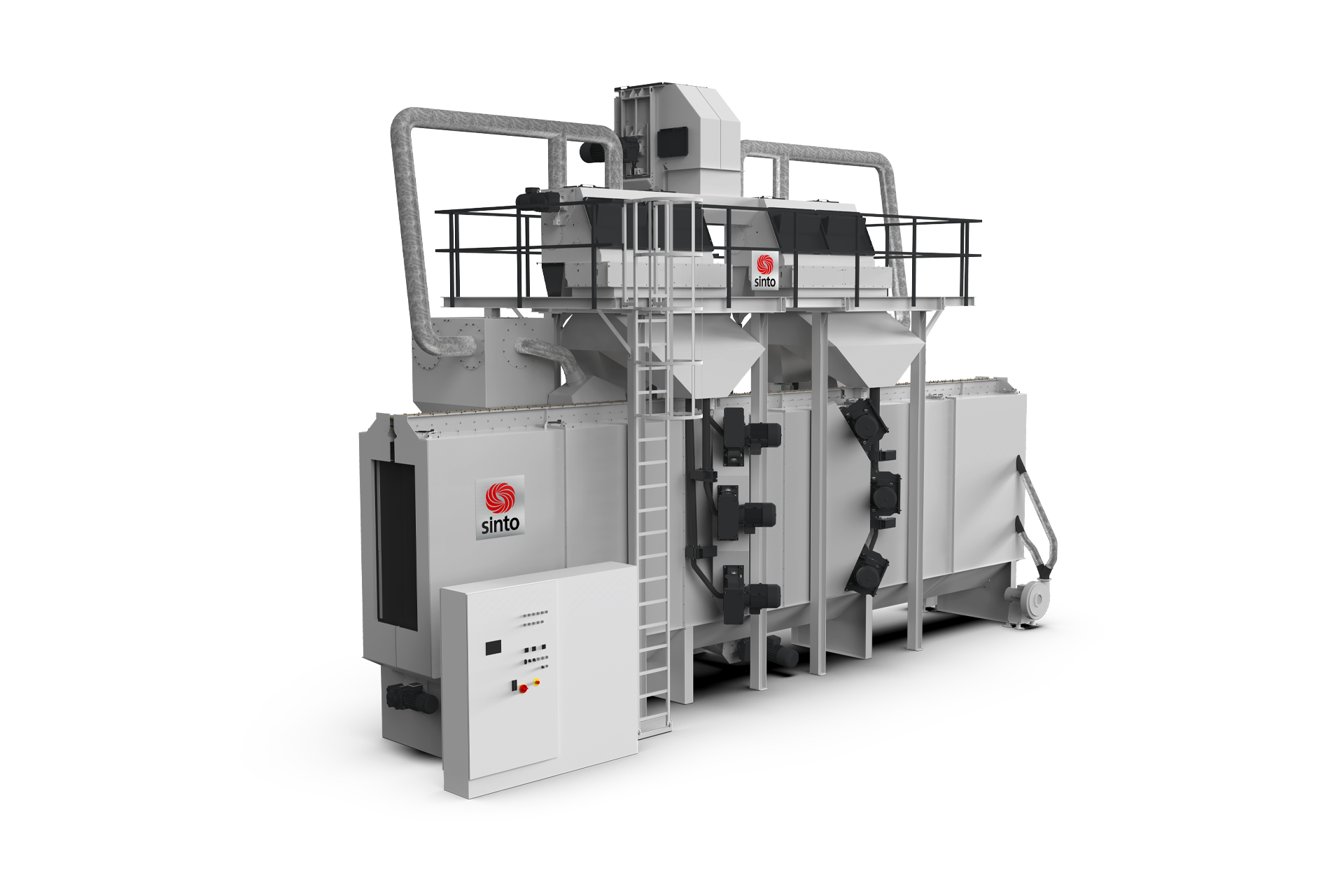
Possible applications for AGTOS continuous overhead rail shot blast machines (type DHT)
Continuous overhead conveyor blast machines are among the most flexible blast machine types. They are used for a variety of workpieces for derusting, descaling, final sanding, deburring and finish blasting of sensitive components or for roughening surfaces for subsequent coating.
The rail guidance of the overhead conveyor system is adapted to local requirements. In many cases, different machining processes such as blasting, painting and subsequent drying can be combined using the overhead conveyor system, thereby exploiting enormous rationalisation potential.
Further variation possibilities arise through the use of different blasting racks with the help of which the workpieces are fed into the machine. In many cases, standard blasting frames with discs, baskets or bars can solve the task. However, the requirements of our customers are always clarified in detail and often lead to a customised solution.
You are currently viewing a placeholder content from YouTube. To access the actual content, click the button below. Please note that doing so will share data with third-party providers.
More InformationContinuous overhead rail shot blast machines Product programme
Our standard programme for continuous overhead rail shot blast machines includes several sizes.
The determination of the suitable machine concept depends, among other things, on the workpieces, the required output and, last but not least, the customer’s ideas regarding an optimised production process.
If the task cannot be solved with a standard machine, we will develop a customised machine concept for you.
Please send us your detailed enquiry.
Our experienced team will be happy to help you.
Type | DHT | DHT | |
---|---|---|---|
Number of high-performance turbines | pcs. | Individual | Individual |
Transport system | Power&Free | Chain conveyor | |
Max. Hakenbelastung | Kg | from 400 | from 400 |
Opening system | Doors | Slats | |
Passage width | mm | Customized | Customized |
Passage height | mm | Customized | Customized |
Automatic cleaning | O | O | |
Free-jet room option | O | X | |
Manual cleaning option | O | X |
Operating sequence for continuous overhead rail shot blast machines
The diagram on the left shows the path of the workpieces through the AGTOS blasting system. You can count on us to always consider the optimal solution for your workpiece. In doing so, we take into account the factors of time, cost and material. This is how you optimise your production.